Zapobieganie korozji
Przewodnik po korozji – część 2
Pierwszą część naszego przewodnika poświęciliśmy różnym typom korozji. Z kolei druga część porusza temat różnych możliwości zapobiegania powodowanym przez nią zniszczeniom.
Ochrona przed korozją zawiera wszystkie środki, jakie pomagają unikać zniszczeń spowodowanych korozją na elementach metalowych. Oprócz elementów odpornych na korozję, istnieje sporo powłok pozwalających zwiększyć poziom ochrony przed nią. Przyjrzyjmy się więc bliżej tym opcjom.
Selekcja surowca
Do surowców zapobiegających korozji należą między innymi metale nieżelazne oraz stale nierdzewne i kwasoodporne. Te ostatnie są również powszechnie określane jako „stale nierdzewne”. Materiały na śruby oznaczone jako odporne na korozję to między innymi odporne na korozję stale nierdzewne według DIN EN 3506 i Dopuszczenie do obrotu i stosowania w budownictwie Z-30.3-6.
Stale nierdzewne tworzą samoodnawiającą się warstwę powierzchniową, powłokę pasywną. Chroni to materiał podstawowy przed korozją. Do wytworzenia powłoki pasywnej konieczne jest odpowiednie stężenie tlenu.
W technice zamocowań stosowane są różne typy stali nierdzewnej, w zależności od obszaru stosowania. Następujące typy stali nierdzewnej są używane szczególnie często:
- Stal nierdzewna gatunku A2 (V2A) i A4 (V4A)
- Stale nierdzewne gatunku HCR (np. 1.4529)
Wykorzystywanie surowców odpornych na korozję jest zatem jedną z dróg do zmniejszenia zniszczeń spowodowanych korozją.
Uwaga dotycząca kombinacji różnych surowców
Podczas łączenia surowców odpornych na korozję, koniecznie musimy zwracać uwagę na korozję bimetaliczną, ze względu na to, że nie wszystkie surowce są ze sobą kompatybilne.
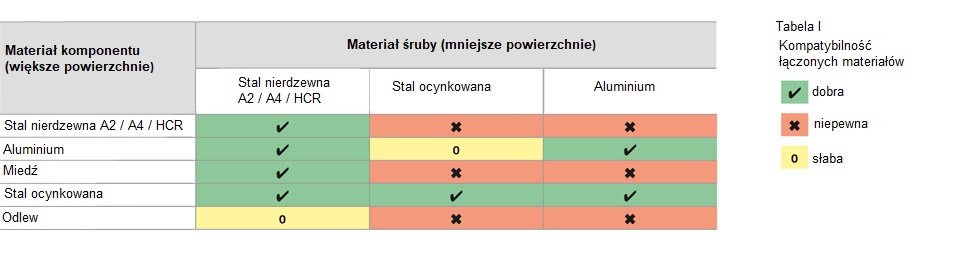
Dobór powłoki
Dzięki odpowiedniej powłoce powierzchnia jest uważana za „zabezpieczoną przed korozją”. Wykorzystanie odpowiednich powłok jest więc uważane za kolejny sposób na redukcję zniszczeń powodowanych przez korozję.
Powłoki powierzchniowe śrub są przeznaczone do powierzchni niemetalicznych i metalowych.
Tak zwane powłoki nakładane galwanicznie lub powłoki cynkowo–lamelarne są generalnie stosowane do ochrony powierzchni metalowych w celu zwiększenia ochrony przed korozją:
Cynkowanie galwaniczne
Najpopularniejszą powłoką metaliczną elementów złącznych jest cynkowanie galwaniczne (5–10 µm) z późniejszą pasywacją. W celu cynkowania detale zanurzane są w elektrolicie cynkowym i odbywają się procesy chemiczne i elektrochemiczne. W kolejnej fazie pasywacji na metalu tworzy się dodatkowa warstwa ochronna, która zapobiega lub znacznie zwalcza korozję.
Wiedza podstawowa
pasywacja to powłoka tlenkowa zawierająca chrom, dostępna w różnych wariantach. Wersja z tlenkiem chromu (VI) okazała się bardzo odporna na korozję, ale jest toksyczna, dlatego należy wykluczyć ten proces. Zgodnie ze specyfikacjami dyrektywy REACH, EJOT stosuje wyłącznie powłoki i pasywacje niezawierające tlenku chromu (VI). Dyrektywa REACH jest uważana za jedną z najbardziej rygorystycznych przepisów dotyczących chemikaliów na świecie, która stanowi, że do stosowania substancji niebezpiecznych wymagane są zezwolenia. Tlenek chromu (VI) nie może być już używany bez odpowiedniego zezwolenia od 2017 roku.
Późniejsze uszczelnienie tak zwaną warstwą nawierzchniową chroni warstwę cynku przed korozją białą rdzą i dodatkowo zwiększa ochronę przed korozją.
Przegląd właściwości i zalet:
- Wszechstronny zakres działań
- Opłacalność procesów
- Odporny na wpływy środowiskowe
- Ochrona przez zniszczeniami spowodowanymi transportem, konfiguracją czy usługami
- Wysoka odporność na korozję
- Doskonałe dalsze przetwarzanie
Powłoka cynkowo – lamelarna
Powłoka cynkowo – lamelarna jest powłoką nieelektrolityczną, składającą się z tak zwanej nieorganicznej powłoki bazowej i nawierzchniowej.
Powłoka bazowa może być powłoką cynkowo–lamelarną, składającą się głównie z cynku i lameli aluminiowej. Jest ona aplikowana bezpośrednio na część metalową. Taka warstwa bazowa określa właściwości antykorozyjne. Cynk zapewnia wysoki poziom katodowej ochrony przed korozją.
Warstwa nawierzchniowa (uszczelniająca) dodatkowo uzupełnia właściwości powłoki bazowej. Oprócz ochrony przed korozją ta powłoka nawierzchniowa chroni przed skutkami chemicznymi i mechanicznymi oraz odpowiada między innymi za odporność na warunki atmosferyczne oraz wygląd.
Kombinacja tych dwóch nazywana jest powłoką dupleksową.
Przegląd właściwości i zalet:
- Długoterminowa ochrona przed korozją pod cyklicznymi obciążeniami
- Zahamowanie tworzenia się czerwonej i białej rdzy oraz korozji galwanicznej
- Brak kruchości wodorowej
- Odporność chemiczna
- Możliwa cienka grubość (6 - 25 µm) powłoki
- Odporność na ciepło (180 - 300 °C w zależności od produktu)
Proces ten stosowany jest wszędzie tam, gdzie doskonałą ochronę antykorozyjną łączy się z innymi właściwościami użytkowymi i dekoracyjnymi.
Zabezpieczenie antykorozyjne w postaci powłoki cynkowo-lamelarnej zostało pierwotnie zaprojektowane jako chromowa alternatywa dla cynkowania. Stało się tak z powodu szerokiego wachlarza dostępnych możliwości dla szerokiego zakresu zastosowań.
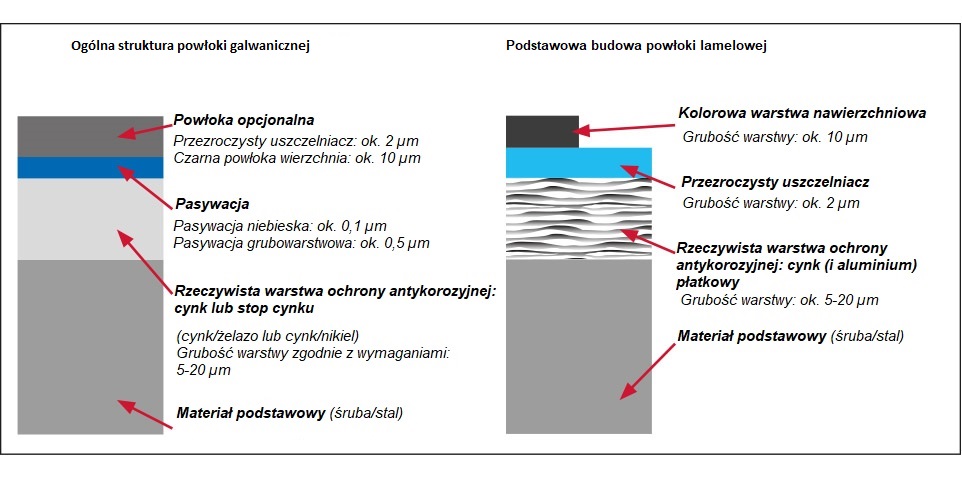
Oprócz cynkowania i powłoki cynkowo-lamelarnej istnieją jeszcze inne rodzaje powłok. Należą do nich powłoki ogniowe, takie jak cynkowanie ogniowe oraz powłoki mechaniczne. Jednakże, ze względu na częściowo duże grubości warstw, w mniejszym stopniu nadają się do wkrętów samogwintujących i samowiercących w sektorze budowlanym.
Oprócz powłok galwanicznych, zgodnie z DIN EN 4042 oraz powłok cynkowo–lamelarnych zgodnie z DIN EN ISO 10683, powłoki dupleksowe C 1000, CLIMADUR i EJOGUARD są wykorzystywane w produktach EJOT.
Dzięki kombinacji specjalnie skoordynowanych powłok, powłoka EJOGUARD oferuje doskonałe właściwości korozyjne. O odporności tysiąca godzin w teście mgły solnej według DIN EN ISO 9227 i piętnastoma cyklami testowymi w teście Kesternicha (test korozyjny z dwutlenkiem siarki i wodą) według DIN 50018, zakres zastosowań metalowych śrub jest znacznie rozszerzony w zależności od krajowych regulacji.